Your basket is currently empty!
This Warehouse Safety tips article provides some tips employers should consider when managing warehouse safety. We cover:
1) The various sources of hazards within a warehouse.
2) Safety measures to be followed while working in a warehouse environment.
Important of Warehouse Safety Management
More than 145,000 people work in over 7,000 warehouses. Unfortunately, the fatal injury rate for the warehousing industry is higher than the national average for all other industries.
The following are hazards that increase risks to warehouse operatives:
- Unsafe use of forklifts
- Improper stacking of products
- Failure to use proper personal protective equipment
- Failure to follow proper lockout/tagout procedures
- Inadequate fire safety provisions
- Repetitive motion injuries
Your organisation is legally required to provide a safe working environment so that staff may carry out their duties in the safest possible manner.
Warehouse Safety Legal Requirements
It is a moral obligation to follow health and safety procedures in warehouses, and a legal requirement.
The Health and Safety at Work Act 1974 requires organisations to provide equipment, information, instruction, training and supervision as necessary to ensure, so far as is reasonably practicable, the health and safety at work of its employees.
Cause of Warehouse Accidents
Most accidents in warehouses usually occur while operating machinery. The areas that are most susceptible to accidents you should consider making safer are:
- 1) Docks – Injuries happen while forklifts run off the dock, products fall on employees or equipment strikes a person.
- 2) Forklifts – Forklift turnovers account for a significant percentage of fatalities every year. About 100 employees are killed and 95,000 injured every year while operating forklifts.
- 3) Conveyers – Workers can get injured when caught in pinch points or in the in-going nip points, are hit by falling products or develop musculoskeletal disorders associated with awkward postures or repetitive motions.
- 4) Materials Storage – Improperly stored materials may fall and injure workers.
- 5) Manual Lifting and Handling – Back injuries may occur from improper lifting or overexertion.
- 6) Hazard Communication – Chemical burns are possible if spills of hazardous materials occur.
- 7) Charging Stations – Fires and explosion risks are possible unless proper guidelines are followed.
- 8) Poor Ergonomics – Improper lifting, repetitive motion or poor design of operations can lead to musculoskeletal disorders at work.
- 9) Other Safety Hazards – Inadequate fire safety provisions, improper use of lockout procedures and failure to wear Personal Protective Equipment also create hazards in workplace.
Warehouse Safety Tips
Here are some tips that may help you make your warehouse safer
1. Exposed or open loading dock doors and other areas that employees could fall 4 feet or more or walk off should be chained off, roped off or otherwise blocked.
2. Floors and aisles are cleared of clutter, electrical cords, hoses, spills and other hazards that could cause employees to trip, slip or fall.
3. Proper work practices are factored into determining the time requirements for an employee to perform a task.
4. Employees performing physical work have adequate periodic rest breaks to avoid fatigue levels that could result in greater risk of accidents and reduced quality of work.
5. Newly-hired employees must receive general ergonomics training and task-specific training.
6. The warehouse is well-ventilated.
7. Employees are instructed on how to avoid heat stress in hot, humid environments.
8. Employees are instructed on how to work in cold environments.
9. The facility has lockout/tagout procedures.
Forklift Safety Tips
Following must be kept in mind while operating a forklift:
1. They should meet the established design and construction requirements.
2. Written approval from the manufacturer has to be obtained for any modifications or additions that affect the capacity and safe operation of the vehicle.
3. Forklifts being used in hazardous locations are appropriately marked and approved for such use.
4. Battery charging is conducted only in designated areas.
5. Appropriate facilities are provided for flushing and neutralizing spilled electrolytes, for fire extinguishing, for protecting charged apparatus from damage by trucks and for ventilation to disperse fumes from gassing batteries.
6. Conveyors, overhead hoists or equivalent materials handling equipment are provided for handling batteries.
7. Reinstalled batteries are properly positioned and secured.
8. Carboy tilters or siphons are used for handling electrolytes.
9. Vent caps are properly functioning. Overhead guards are provided in good condition to protect forklift operators from falling objects.
10. Tools and other metallic objects are kept away from top of uncovered batteries.
11. Precautions are taken to prevent smoking, open flames, sparks or electric arcs in battery changing areas and during storage/ changing of propane fuel tanks.
Warehouses with Hazardous Substances
Hazardous spills must be taken care of to prevent chemical burning. Some of the safety measures to be followed include:
1. All hazardous material containers are properly labelled indicating the chemicals identity and appropriate warnings.
2. The facility should have a written programme that covers hazard determination, including Material Safety Data Sheets (MSDSs), labelling and training.
3. There is a system to check that each incoming chemical is accompanied by an MSDS.
4. All employees must be adequately trained to handle chemicals and understand MSDS and on precautions to take to prevent exposure.
5. All outside contractors are given a complete list of chemical products, hazards and precautions.
6. All chemicals are stored according to the manufacturers recommendations and local or national fire codes.
9. Employees must use Personal Protection Equipment while handling hazardous chemicals.
Warehouse Safe Storage
For most of the hazards related to warehouse safety, making simple changes can help improve safety for example;
- Adjusting the height of shelves
- Providing stools or ladders to employees
- Reducing the depth of shelving
- Raising loading heights
- Evaluating the flow and volume of orders so faster-moving products are placed on easier-to-reach shelves
- Safe packing of all materials will ensure that accidents from material spillage and falling are reduced to minimum.
Warehouse Risk Assessments
The warehouse manager carries out a risk assessment of the warehouse. To identify the hazards, this should include:
- Identifying where hazards can occur
- Walking around the warehouse noting activities that might pose a risk
- Talking through the issues with the union safety representative and asked about concerns that staff have on health and safety
- Talking to supervisors to learn from their detailed knowledge of particular jobs and areas
- Looking at the accident book to gather information on past problems
- The identification of each hazard should be followed by studying the control factors and comparing them to a good practice guidance or manual. Actions necessary to manage the risks should be written down and any further actions implemented.
This ends the Warehouse Safety Tips article
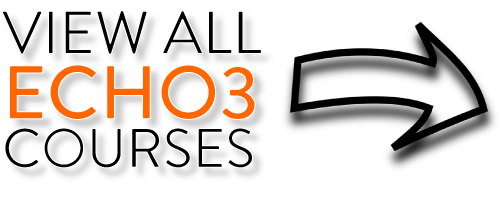